FONDERIA MARIANI
Fonderia Mariani was founded in 1952 by Claudio Mariani.
Since its inception, the foundry has evolved from a modest workshop to become one of the premier artistic bronze casting facilities globally. Through groundbreaking experiments and inventive techniques, the foundry has perfected unique methods, enabling it to undertake highly complex castings. With extensive experience and technical expertise, it stands as a cornerstone in the field of bronze casting, providing invaluable support to numerous artists who entrust their creations to this esteemed foundry.
The Mariani foundry primarily focuses on artistic casting and has established collaborations with several internationally renowned artists, including the late Fernando Botero and Igor Mitoraj. Additionally, numerous Danish artists, such as Peter Brandes, Maja Lisa Engelhardt, Christian Lemmerz, Bjørn Nørgaard, Kirsten Ortwed, and many others, both established and emerging talents, choose to produce their work at Mariani in collaboration with us
The foundry's extensive collaboration and ongoing dialogue with artists position it at the forefront of artistic casting, leading to numerous innovative projects over the years. Presently, the foundry is under the leadership and ownership of the Agolini family, who assumed control of the foundry through familial connections back in the 90s.
MAGNIFICATION AND MOLDS
The model for a bronze sculpture is not always created in a 1:1 scale. Therefore, the sculpture often originates from a smaller model, which is then scaled up to the final dimensions of the sculpture. The foundry possesses considerable experience and expertise in this process. Using materials such as plaster or clay, a new model is crafted, and once it has achieved its intended dimensions, an impression is made in rubber and plaster, forming the mold for casting. The foundry maintains its own workshop for mold-making, allowing artists to engage in the process from its early stages.
WAX
The initial step in crafting a bronze sculpture involves creating a wax replica of the actual sculpture. This process utilizes molds based on the full-size model. Smaller sculptures are reproduced to scale, while larger ones are divided into multiple parts. This methodology extends to the casting phase as well. By working with wax models, artisans can refine and manipulate the sculpture to precisely match the artist's vision. This stage of the process offers artists maximum involvement and influence over the final product in collaboration with the foundry. Subsequently, the wax model serves as the basis for creating a ceramic mold for casting. The advantage of using wax lies in its ability to be easily melted out of the mold and reused for other sculptures.
CERAMIC COATING
The wax replica is now covered by a thin layer of liquid ceramic coating on all surfaces, meticulously capturing every detail of the wax sculpture. This meticulous process ensures optimal results for the final bronze work. Once the ceramic coating has dried and enveloped the wax, the newly formed ceramic molds are fired in a kiln. This process hardens the ceramic layer while simultaneously melting away the wax for future reuse. Once the wax is removed, a new negative mold is revealed, ready to be utilized for the bronze casting process.
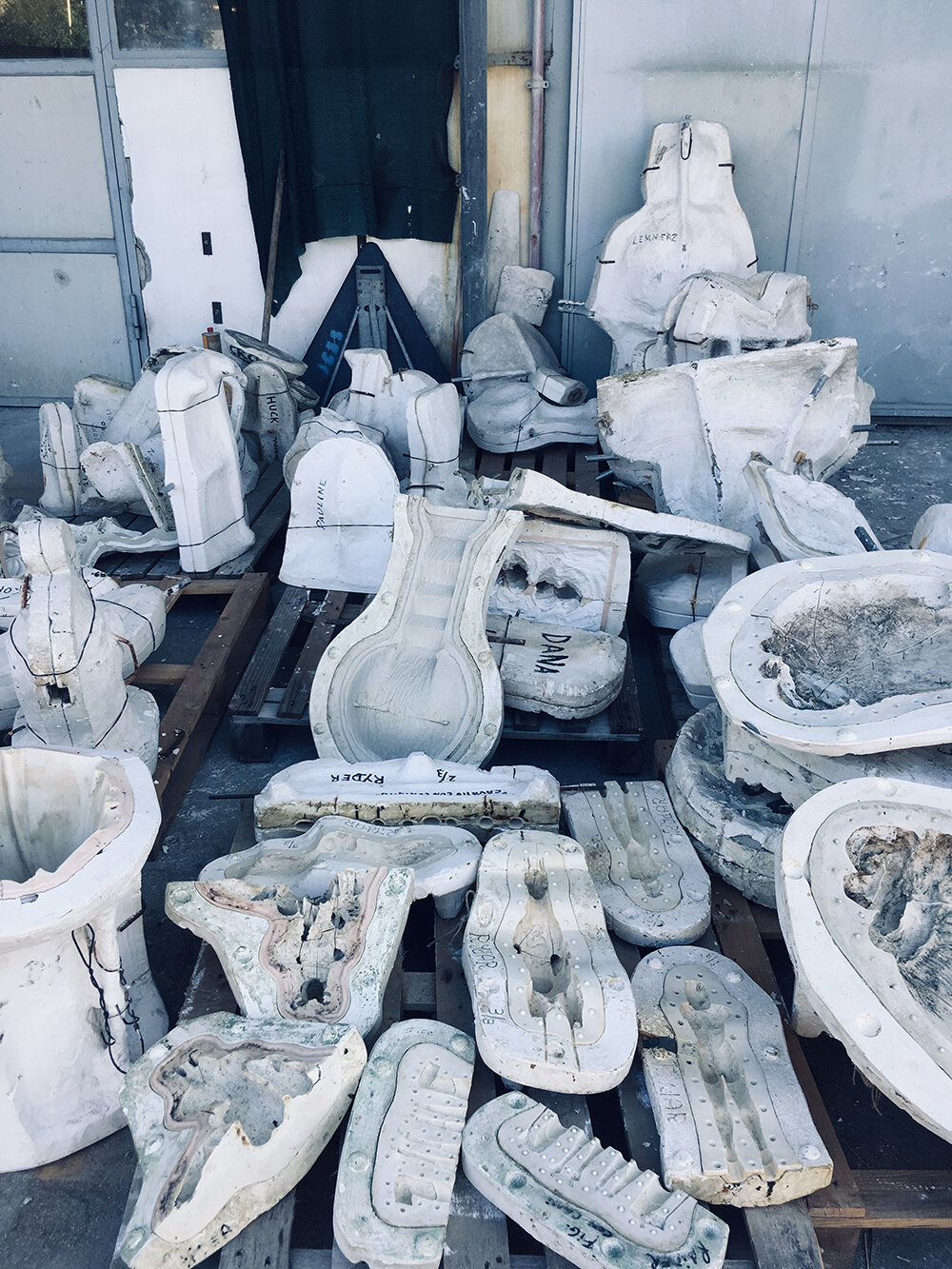


CASTING
The bronze is carefully poured into the ceramic mold placed within suitable containers filled with sand. The sand serves to ensure both safety during production and stability for the ceramic mold. As the molten bronze flows into the mold, it faithfully replicates every detail of the original wax model. After the bronze has cooled and solidified, the ceramic coating is removed from the bronze sculpture. Subsequently, the sculpture undergoes sandblasting and preparation for the subsequent stages of the process.
RETOUCHING
Before the casted bronze sculptures enter the final stage, they undergo a process in the retouching workshop. Here, any residual bronze left over from the casting process is removed from the surface of the sculpture. These remnants typically consist of tubes and cubes initially formed in wax to guide the flow of bronze into the ceramic mold. Although these tubes and cubes are also casted in bronze, they are not part of the final sculpture. Subsequently, the surface of the sculpture is meticulously retouched and polished. If the sculpture consists of multiple parts, they are welded together during this phase. With the sculpture nearly completed, it then proceeds to the patination workshop before leaving the foundry.
PATINATION
In the foundry's patination workshop, the desired patina for the surface of the sculpture is carefully chosen. Initially, patination serves as a protective layer for the metal, achieved through oxidation with chemicals. However, it is also an opportunity to impart specific colors or hues to the bronze surface. This can vary from traditional bronze tones to shades of blue, green, or other desired colors.

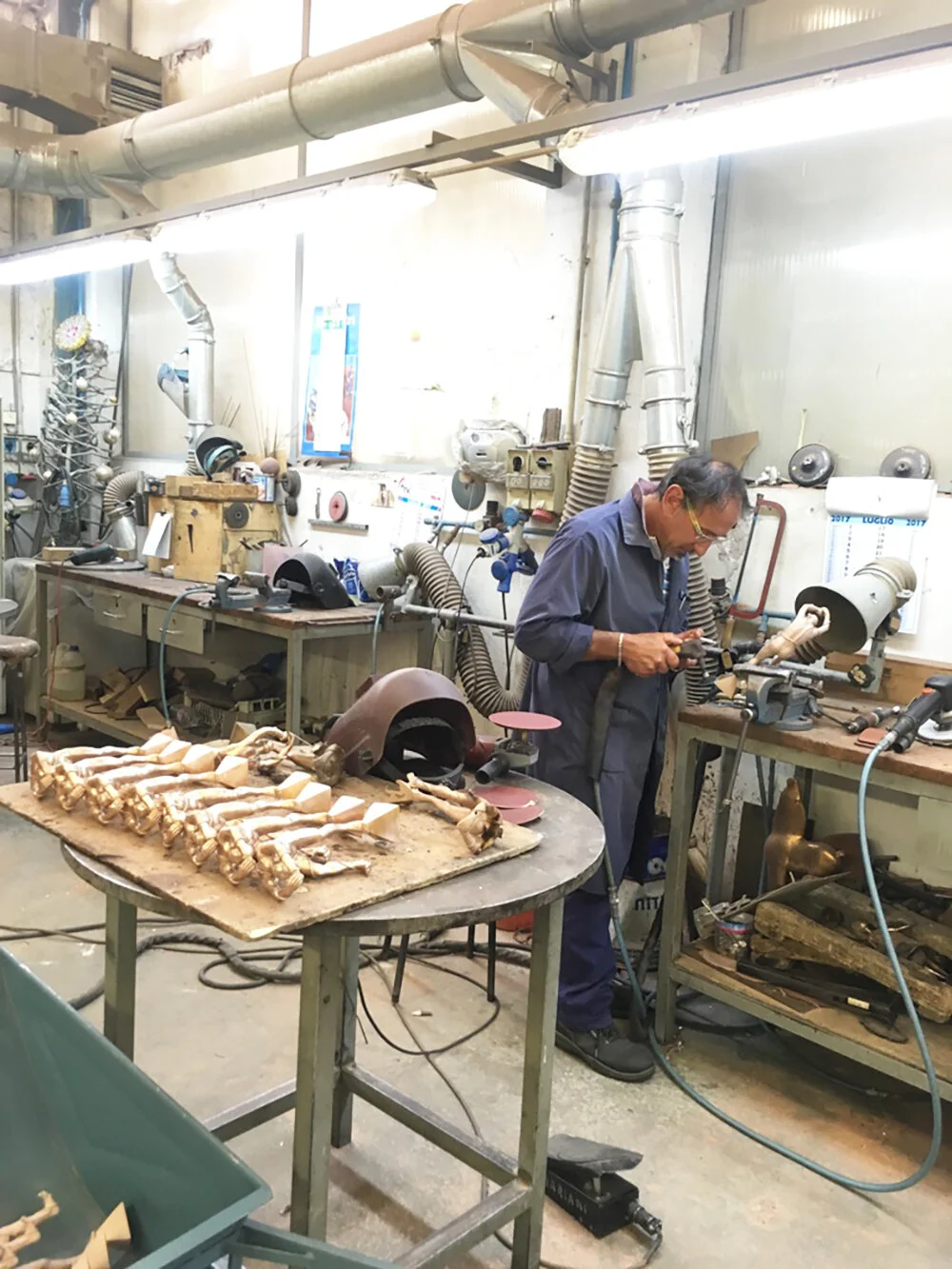
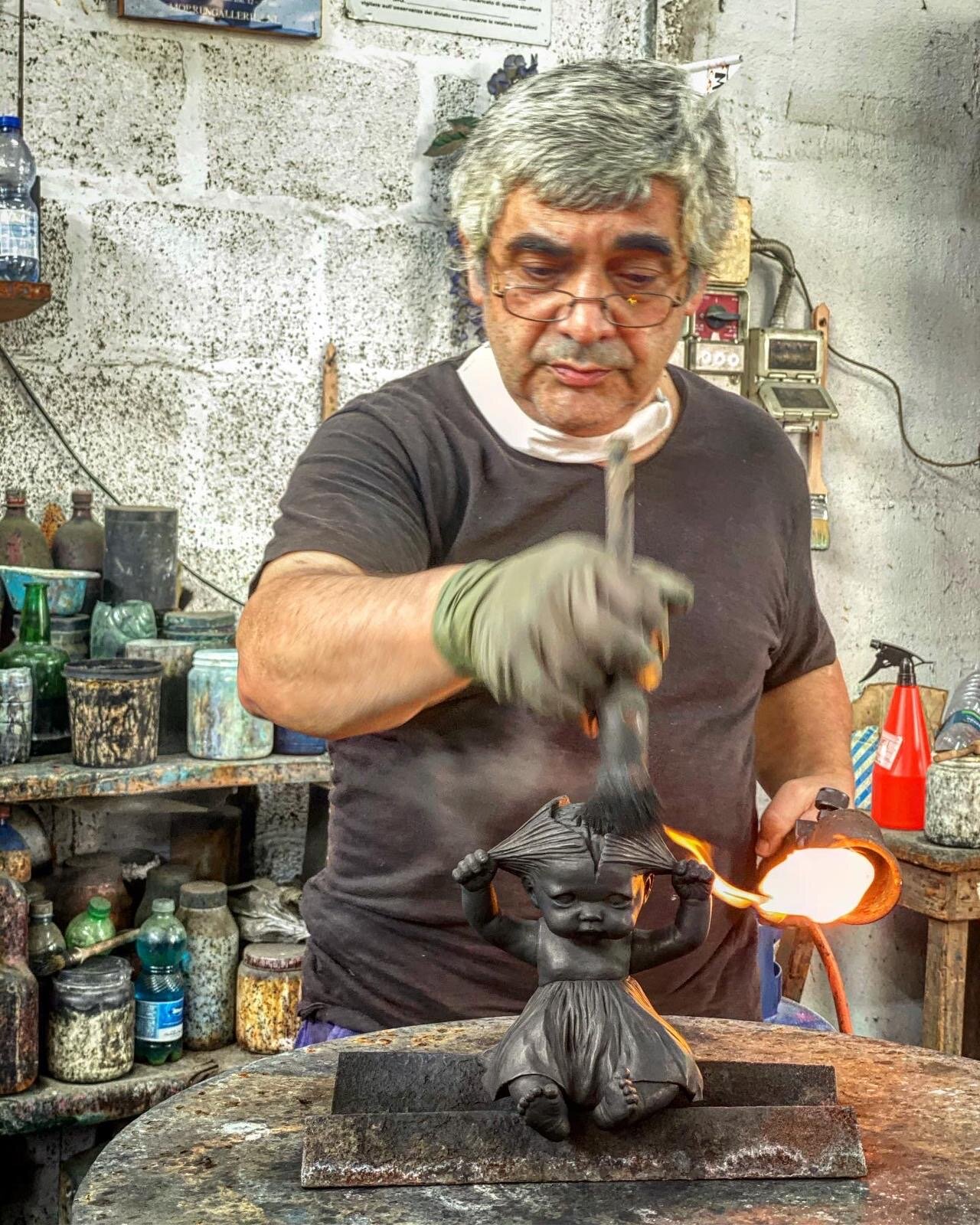